Introduction to the History of Concrete
Concrete is everywhere: from the foundations of our homes and the pillars of our bridges to the sculptures that adorn public spaces.
Yet few pause to consider the astonishing journey behind this ubiquitous material. The history of concrete spans millennia, tracing a path from rudimentary mud and straw mixtures to ultra high performance blends that can self-heal cracks.
In this article, we’ll explore ten pivotal milestones – ancient inventions, ground-breaking patents, industrial revolutions, and cutting edge green technologies – that have defined the evolution of concrete.
Along the way, we’ll touch on Roman concrete, Portland cement, reinforced concrete, pozzolanic ash, green building, and 3D-printed concrete.
By the end, you’ll appreciate not only how concrete shapes our world, but also how it continually reinvents itself to meet tomorrow’s challenges.
1. Early Beginnings: The Origins of Concrete
Long before engineers and architects, our ancestors stumbled upon the benefits of binding materials to create more durable surfaces.
In Mesopotamia and Egypt, as early as 6500 BC, builders mixed mud, sand and straw to form rudimentary bricks and flooring throughout the history of concrete.
By around 3000 BC, the ancient Egyptians had advanced to stock breeding gypsum and lime mortars in the construction of pyramids and temples, laying a primitive yet vital foundation for subsequent developments.
These early binders relied on readily available materials: crushed limestone, volcanic ash, clay, and naturally occurring bitumen.
Although lacking the mechanical strength of modern mixes, they offered a glimpse of the transformative power held within mineral chemistry.
Over centuries, craftsmen experimented with proportions and aggregates – crushed stone, pottery shards, and even animal hair, gradually refining their formulas.
This trial and error phase planted the seeds for the sophisticated cementitious materials to come.

2. Concrete in Ancient Civilisations
The History of Concrete in Ancient Rome
When we think of ancient builders, Roman engineers immediately spring to mind.
Their creation of opus caementicium – a hydraulic cement combining lime, water, volcanic ash (pozzolana), and aggregate – was nothing short of revolutionary.
This mix enabled the construction of awe-inspiring structures like the Pantheon’s unreinforced dome, still the world’s largest of its kind nearly two millennia later.
Key to Roman success was pozzolana, a fine volcanic ash sourced from regions such as Pozzuoli near Naples.
When slaked lime is blended with pozzolana, it undergoes a chemical reaction forming strong, durable calcium-silicate hydrates.
Roman builders even added seawater to mixtures for harbour works, allowing underwater setting.
The longevity of Roman concrete, evidenced in aqueducts and breakwaters, stems from its unique microstructure and self-healing mineral growth.
3. The Decline and Rediscovery of Ancient Techniques
Following the fall of the Western Roman Empire around 476 AD, much technical knowledge around the history of concrete was lost.
For centuries, Europe reverted to stone, brick, and timber construction, with lime mortars playing a supporting role.
The formula for durable hydraulic cement disappeared into obscurity.
It wasn’t until the Renaissance – spurred by renewed interest in classical antiquity, that scholars rediscovered Vitruvius’s texts outlining Roman methods and the history of concrete.
Architects such as Filippo Brunelleschi studied ancient ruins, reintroducing lime based mortars in Florence and Venice.
Nevertheless, the precise composition of Roman concrete remained elusive until modern scientific analysis in the 20th and 21st centuries confirmed the importance of pozzolanic reactions and microcrystalline development.

4. The Birth of Modern Cement: Portland Cement (1824)
The true genesis of modern concrete began in 1824 when British bricklayer Joseph Aspdin patented Portland cement, so named because its colour and durability resembled high quality Portland stone.
Aspdin heated a mixture of limestone and clay to high temperatures in a kiln, then ground the clinker to a fine powder.
This innovation provided a consistent, hydraulic cement that set quickly and could be mass produced.
In the decades that followed, advances in kiln design and raw material grinding enabled large scale manufacture and started to change the history of concrete and the projected future.
By the late 19th century, Portland cement was the cornerstone of the booming construction industry in Europe and North America, finding uses in roads, canals, railways, and public buildings.
5. The Industrial Revolution and Concrete Infrastructure
With the advent of steam power and mechanisation, the mid-19th century saw an explosion in cement production.
Railways, bridges and docks demanded resilient, affordable materials.
Concrete – now based on Portland cement, delivered on both counts.
Notable projects in the history of concrete included:
- The Thames Tunnel (opened 1869): the first underwater tunnel, employing concrete linings for structural support.
- The Suez Canal (completed 1869): used concrete to stabilise banks and lock chambers.
- Early concrete bridges: spanning rivers across Europe and the United States, demonstrating concrete’s versatility.
This era cemented (pun intended) concrete’s role as the backbone of modern infrastructure, ushering in an age of unprecedented connectivity and urban growth.
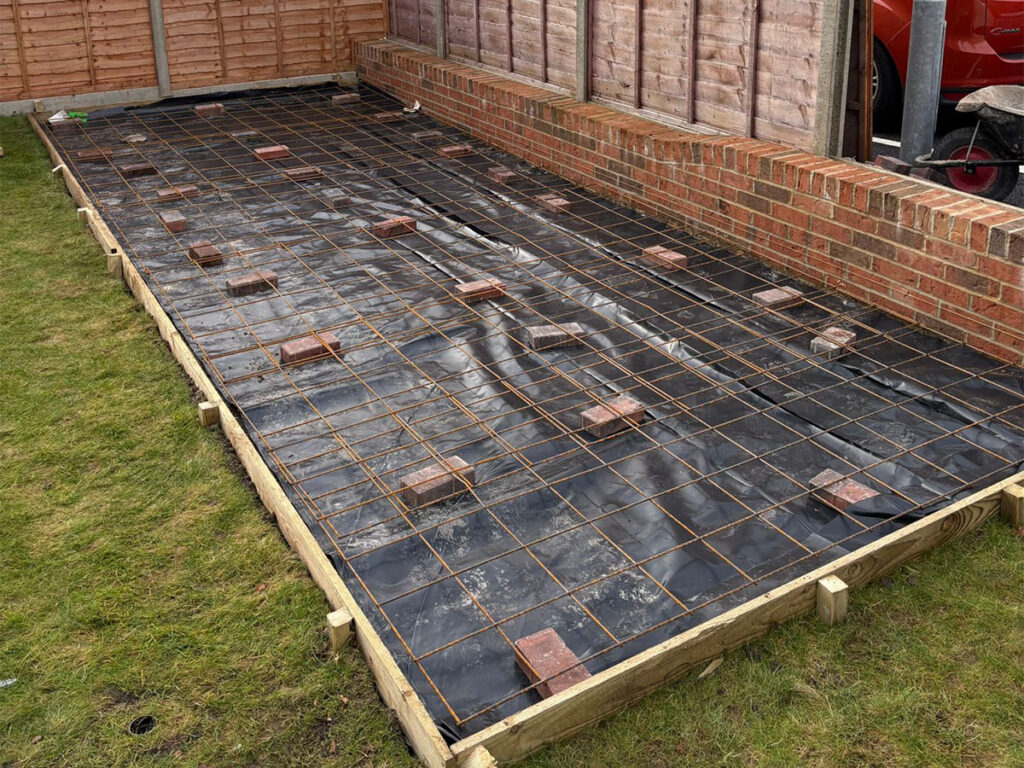
6. Reinforced Concrete: Merging Steel and Cement
The union of steel and concrete around 1867 ushered in perhaps the most significant advancement since Roman times.
Frenchman Joseph Monier patented iron reinforced concrete flowerpots, but it was engineer François Hennebique who, in 1892, formalised a system for reinforced concrete beams, slabs, and columns.
By embedding steel bars within concrete, builders combined concrete’s compressive strength with steel’s tensile resilience.
Reinforced concrete allowed for slimmer profiles, longer spans, and taller structures.
It gave rise to the first skyscrapers, changing the history of concrete and the skyline – buildings that could resist both gravity loads and lateral forces like wind and earthquakes.
Iconic early examples include:
- Ingalls Building (Cincinnati, 1903): the world’s first reinforced concrete skyscraper.
- Johnson Wax Building (Wingspread, 1939): showcasing organic forms achievable with reinforced concrete.

7. Concrete in the 20th Century: Skyscrapers and Dams
The 20th century witnessed concrete’s golden age in the history of concrete.
Architects and engineers pushed its limits:
- Hoover Dam (completed 1936): one of the largest mass concrete structures ever built, using over 3 million cubic metres of concrete.
- Empire State Building (completed 1931): concrete foundations underpinning the iconic steel frame.
- Unité d’Habitation (Marseille, 1952): Le Corbusier’s brutalist housing block, emphasising raw concrete as an aesthetic.
Post-war reconstruction in Europe and the UK relied heavily on concrete for rapid housing and infrastructure projects.
Prefabricated concrete panels became commonplace, expediting construction and reducing costs.
8. Modern Architecture and Precast Concrete
In the latter half of the 20th century, precast and prestressed concrete transformed building practices.
Factories churned out wall panels, beams, and modular units that were then assembled on site.
This method improved quality control, cut waste, and slashed construction times compared to previous methods in the history of concrete.
Architectural movements like Brutalism celebrated exposed concrete (“béton brut”), valuing its raw texture and sculptural potential.
Landmark examples:
- Barbican Estate (London, completed 1982): a sprawling complex of residences, theatres, and schools.
- Trellick Tower (London, completed 1972): Ernő Goldfinger’s emblem of high-rise living.

9. Technological Advances: UHPC and Self-Healing Concrete
The 21st century has seen concrete evolve into a high tech material:
- Ultra High Performance Concrete (UHPC): With compressive strengths exceeding 150 MPa, UHPC enables ultra thin sections and complex forms.
- Self-Healing Concrete: Embeds bacteria or microcapsules that precipitate calcium carbonate when cracks appear, autonomously sealing them.
- 3D-Printed Concrete: Robotic printers deposit layers of custom designed concrete, allowing free form architecture and rapid on site fabrication.
These innovations address challenges of durability, material efficiency, and design freedom, heralding a new era and history of concrete construction.
10. Environmental Impact and the Rise of Green Concrete
Despite its versatility, concrete carries an environmental price tag: cement production accounts for around 8% of global CO₂ emissions.
Tackling this, researchers and industry have developed green concrete alternatives:
- Fly-ash and Slag Blends: Replace a portion of cement with by-products of coal and steel production, reducing embodied carbon.
- Carbon-capture Technologies: Sequester CO2, the process of capturing and storing atmospheric carbon dioxide (CO2), during curing, converting it into stable mineral forms.
- Recycled Aggregates: Use crushed demolition waste instead of virgin stone.
Governments and standards bodies are now promoting low-carbon cements, driving innovation toward net-zero concrete, forever changing the history of concrete.
Frequently Asked Questions
Q: What is concrete made of?
A: Traditional concrete comprises Portland cement, water, fine aggregate (sand), and coarse aggregate (gravel or crushed stone). Modern mixes may include supplementary cementitious materials like fly-ash, slag, silica fume, and additives to modify properties such as workability, strength, and durability.
Q: When was concrete first invented?
A: While rudimentary cementitious materials in the history of concrete date back to 6500 BC in the Middle East, Roman concrete around 300 BC represents the first truly hydraulic binder, able to set under water.
Q: Why was Roman concrete so durable?
A: The use of volcanic pozzolana and lime resulted in chemical reactions forming strong calcium-silicate hydrates. Marine exposure encouraged the growth of minerals like aluminous tobermorite, which sealed cracks over time.
Q: How is modern concrete different from ancient concrete?
A: Modern concrete uses precisely manufactured Portland cement and industrial aggregates, ensuring consistency and higher compressive strengths. Ancient concretes relied on local materials and manual mixing, leading to variable quality.
Q: What is reinforced concrete?
A: Reinforced concrete embeds steel bars (rebar) within the concrete matrix. The concrete handles compressive forces, while steel resists tensile loads, enabling slender and resilient structural forms.
Q: What is green concrete?
A: Green concrete minimises environmental impact by substituting part of the cement with industrial by-products, using recycled aggregates, or capturing CO2 in the curing process.
Q: What is concrete used for in modern times for homeowners?
A: Today, homeowners rely on concrete for a wide range of practical and aesthetic applications, including:
- Foundations and Footings: Providing a stable, durable base for houses and extensions.
- Driveways and Walkways: Durable surfaces that withstand vehicle loads and foot traffic; often enhanced with sealants to resist staining and weathering.
- Patios and Outdoor Living Spaces: Smooth or textured slabs, frequently stamped or stained for decorative effect.
- Garage Floors and Shed Slabs: Tough surfaces resistant to oil, moisture, and heavy loading.
- Countertops and Interior Flooring: Polished or stained concrete offers a modern, low maintenance finish.
- Retaining Walls and Planters: Structural and decorative elements in landscaping, helping control soil erosion and define garden spaces.
- Pool Decks and Outdoor Kitchens: Slip resistant and UV-stable surfaces that integrate seamlessly with home exteriors.
By combining strength, versatility, and design flexibility, concrete remains one of the most popular materials for homeowners looking to enhance both function and curb appeal.